The Unseen Bonds: A Deep Dive into Automotive Interior Adhesives
In the relentless pursuit of enhanced safety, comfort, and aesthetics, the modern automotive interior has evolved into a sophisticated symphony of materials. From the plush feel of a dashboard to the seamless integration of electronic components, the integrity and performance of these elements hinge critically on a class of unsung heroes: automotive interior adhesives. Far more than simple glues, these advanced formulations are meticulously engineered to meet the demanding requirements of the automotive environment, playing a pivotal role in everything from structural integrity to noise reduction and passenger well-being.
The Multifaceted Role of Adhesives in Automotive Interiors
Automotive interior adhesives are not a monolithic category. Instead, they encompass a diverse range of chemistries and applications, each tailored for specific bonding challenges. Their functions are extensive and critical:
- Structural Bonding: Many interior components, such as dashboard assemblies, door panels, and headliners, rely on adhesives for their structural integrity. These bonds must withstand significant stress, vibration, and temperature fluctuations without delamination or failure.
- NVH (Noise, Vibration, and Harshness) Reduction: Adhesives with viscoelastic properties are crucial in dampening vibrations and absorbing sound, contributing significantly to a quieter and more comfortable cabin. This is particularly evident in applications like bonding sound-deadening mats and sealing gaps.
- Aesthetic Integration: Seamless transitions between different materials, flush mounting of trim pieces, and the elimination of unsightly fasteners are all achieved through precise adhesive application, contributing to the premium look and feel of modern interiors.
- Safety and Durability: Adhesives contribute to the overall crashworthiness of a vehicle by ensuring components remain in place during an impact. Furthermore, they provide long-term durability, resisting degradation from UV exposure, humidity, and cleaning agents.
- Lightweighting: As the automotive industry pushes for lighter vehicles to improve fuel efficiency and reduce emissions, adhesives offer a compelling alternative to traditional mechanical fasteners. By distributing stress more evenly across bonded surfaces, they can allow for the use of thinner, lighter substrates.
- Component Assembly and Sealing: From attaching wiring harnesses and electronic modules to sealing HVAC ducts and airbag compartments, adhesives provide efficient and reliable solutions for a myriad of assembly and sealing tasks.
Key Adhesive Chemistries and Their Applications
The selection of an appropriate adhesive chemistry is paramount, driven by the specific substrates to be bonded, the required performance characteristics, and the manufacturing process. Some of the most common chemistries employed in automotive interior applications include:
- Polyurethane (PU) Adhesives: Known for their excellent adhesion to a wide range of substrates, including plastics, metals, and composites, polyurethanes offer good flexibility, impact resistance, and sound dampening properties. They are widely used for bonding headliners, door panels, and general assembly.
- Acrylic Adhesives: These offer fast cure times, high bond strength, and good resistance to environmental factors. Modified acrylics are particularly effective for bonding challenging substrates like low-surface-energy plastics and for structural applications where high initial tack is required. They are often found in trim attachment and emblem bonding.
- Epoxy Adhesives: Epoxies provide exceptionally high bond strength, excellent chemical resistance, and good thermal performance. While typically more rigid, specialized toughened epoxies can offer improved flexibility. They are often used for structural bonding of stronger components and where high durability is critical.
- Hot-Melt Adhesives: These thermoplastic adhesives are applied in a molten state and solidify rapidly upon cooling, allowing for fast assembly processes. They are commonly used for bonding fabrics, foams, and non-structural components like carpet backing and decorative trim, prized for their speed and cost-effectiveness.
- Cyanoacrylate Adhesives (Super Glues): Known for their extremely rapid curing at room temperature, cyanoacrylates are ideal for small, quick bonding tasks and for fixturing components before a more permanent adhesive cures. They are often used for bonding small plastic or rubber parts.
- Pressure Sensitive Adhesives (PSAs): Often supplied in tape form, PSAs provide immediate tack and bond strength upon contact. They are widely used for attaching emblems, trim strips, wiring clips, and sound-deadening materials due to their ease of application and clean finish.
Factors Influencing Adhesive Selection and Performance
Beyond the basic chemistry, several critical factors influence the selection and ultimate performance of automotive interior adhesives:
- Substrate Compatibility: The adhesive must effectively bond to the specific materials involved (e.g., PP, ABS, PC, leather, fabric, metal, wood). Surface energy, porosity, and presence of contaminants all play a role.
- Environmental Resistance: Adhesives must withstand the harsh automotive environment, including temperature extremes (from freezing winters to scorching summers), humidity, UV radiation, and exposure to cleaning agents and chemicals.
- Application Method: Adhesives can be applied via various methods, including dispensing, spraying, rolling, and automated robotic systems. The adhesive's viscosity, pot life, and cure time must be compatible with the chosen manufacturing process.
- Cure Mechanism and Time: Adhesives can cure through various mechanisms (e.g., moisture cure, heat cure, UV cure, anaerobic cure). The cure time directly impacts production line speed and efficiency.
- Mechanical Properties: Required properties include tensile strength, shear strength, peel strength, elongation, and flexibility. These are dictated by the specific application and the stresses the bond will endure.
- NVH Performance: For applications requiring sound damping or vibration isolation, the adhesive's viscoelastic properties are crucial.
- Flammability and VOC Emissions: Adhesives must comply with strict automotive regulations regarding flammability (e.g., FMVSS 302) and low volatile organic compound (VOC) emissions to ensure passenger safety and air quality within the cabin.
- Cost-Effectiveness: Balancing performance requirements with material and application costs is always a key consideration in automotive manufacturing.
The Future of Automotive Interior Adhesives
The automotive industry is in a constant state of evolution, and interior adhesives are no exception. Future trends and developments are likely to focus on:
- Increased Sustainability: Demand for bio-based adhesives, recyclable formulations, and solutions with reduced environmental impact throughout their lifecycle.
- Enhanced Performance for Advanced Materials: As new, lightweight composites and recycled materials become more prevalent, adhesives will need to evolve to provide robust and durable bonds.
- Integration with Smart Interiors: Adhesives will play a role in bonding flexible electronics, sensors, and ambient lighting components, contributing to the development of highly integrated and interactive interior spaces.
- Automation and Robotics: Further advancements in adhesive dispensing and curing technologies will enable even greater automation in manufacturing processes, leading to increased efficiency and consistency.
- Multi-Material Bonding: The growing trend of using dissimilar materials within the same assembly will necessitate adhesives capable of creating strong, durable bonds between a wider variety of substrates.
Conclusion
Automotive interior adhesives, though often unseen, are fundamental to the safety, comfort, and aesthetic appeal of modern vehicles. From their role in structural integrity and NVH reduction to enabling lightweighting and complex component assembly, these sophisticated formulations are indispensable. As the automotive landscape continues to transform with new materials, advanced manufacturing processes, and increasingly sophisticated interiors, the innovation in adhesive technology will undoubtedly remain at the forefront, creating stronger, safer, and more pleasant driving experiences for years to come.
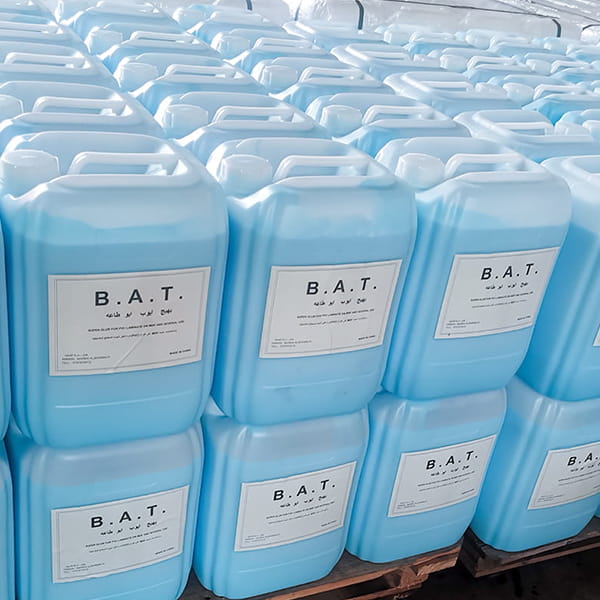