Unlocking the Potential of PUR Flat Lamination Hot Melt Adhesive in Custom Applications
In the realm of industrial bonding, few technologies have captured the imagination of engineers and designers quite like Polyurethane Reactive (PUR) flat lamination hot melt adhesive. With its unparalleled ability to bond diverse materials and deliver exceptional performance, this adhesive is proving to be a game-changer for custom applications across various sectors.
A Closer Look at PUR Technology
PUR flat lamination hot melt adhesive operates on a simple yet ingenious principle: it reacts with moisture in the air to form a permanent, cross-linked bond. This curing process sets it apart from traditional thermoplastic hot melts, which merely cool and harden. The result is a bond that is not only stronger but also more resilient to environmental factors such as heat, humidity, and chemical exposure.
This adaptability makes PUR adhesives particularly suited for custom applications where standard bonding solutions fall short. For instance, in the production of luxury packaging, PUR adhesives ensure that intricate designs and delicate materials remain securely bonded, even when subjected to rigorous handling during shipping and storage.
Custom Applications Across Industries
One of the most exciting aspects of PUR flat lamination adhesives is their potential to unlock new possibilities in niche markets. Take the electronics industry, for example. As devices become thinner and lighter, manufacturers face the challenge of bonding components without adding bulk or compromising structural integrity. PUR adhesives excel in this context, offering precise application and strong, flexible bonds that can accommodate the stresses of daily use.
Similarly, in the textile industry, PUR adhesives are being used to laminate fabrics for high-performance apparel and upholstery. These adhesives maintain the natural drape and feel of the fabric while providing the durability needed for heavy-duty applications. From waterproof outdoor gear to fire-retardant upholstery, the possibilities are virtually endless.
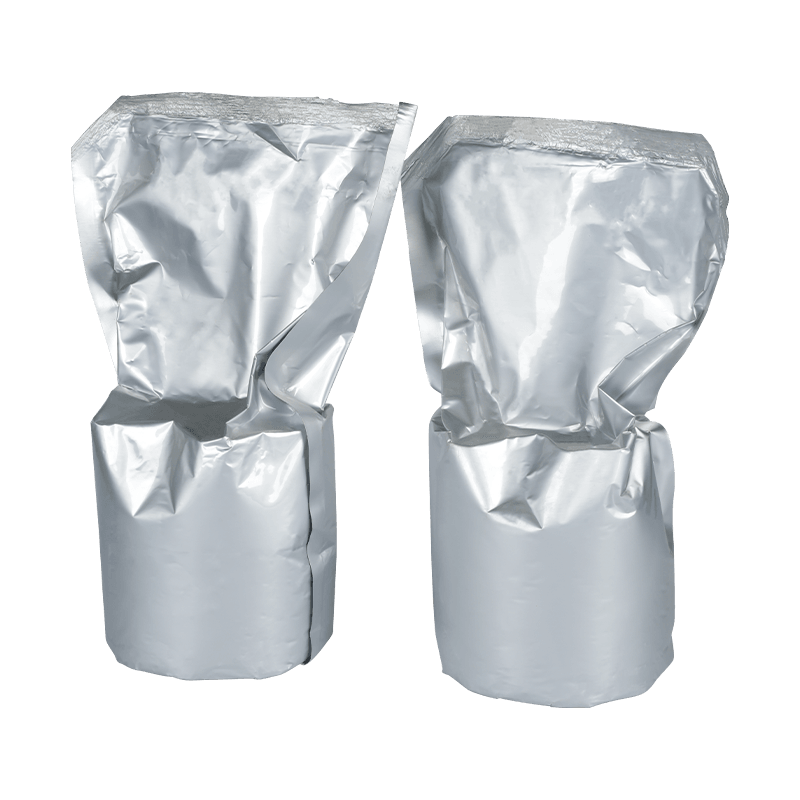
Even the burgeoning field of renewable energy has found a use for PUR adhesives. In solar panel manufacturing, for example, these adhesives are employed to bond protective layers to photovoltaic cells, ensuring optimal performance and longevity. Their resistance to UV radiation and temperature fluctuations makes them an ideal choice for this demanding application.
Overcoming Challenges with Innovation
While the benefits of PUR flat lamination adhesives are clear, their implementation does come with certain challenges. For one, the curing process requires careful control of environmental conditions, particularly humidity levels. Manufacturers must invest in proper equipment and training to ensure consistent results.
Additionally, the initial cost of PUR adhesives can be higher than that of traditional alternatives. However, many companies find that the long-term benefits—such as reduced maintenance, improved product quality, and enhanced customer satisfaction—far outweigh the upfront investment.
To address these challenges, adhesive suppliers are continually innovating. New formulations are being developed to cure faster and perform better under a wider range of conditions. Meanwhile, advancements in application equipment are making it easier than ever for manufacturers to integrate PUR adhesives into their workflows.
The Future of Bonding
As industries evolve and consumer expectations rise, the demand for innovative bonding solutions will only continue to grow. PUR flat lamination hot melt adhesive represents the cutting edge of this trend, offering a combination of strength, flexibility, and versatility that is unmatched by traditional adhesives.
By embracing this technology, manufacturers can push the boundaries of what’s possible, creating custom applications that were once thought unattainable. Whether you’re designing the next generation of wearable tech, crafting bespoke furniture pieces, or engineering sustainable energy solutions, PUR adhesives provide the foundation for success.